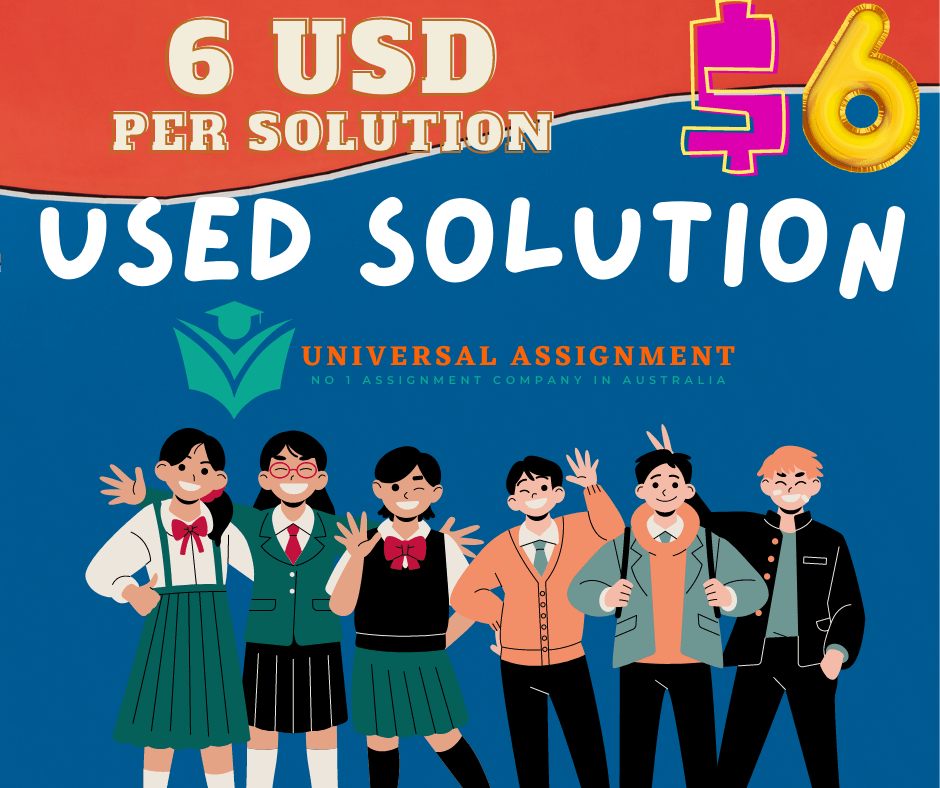
Assignment Task (Assignment Number: UA514)
Mechanical design 1 (48600) 2021 Warman Prototype Designs
4 artefacts to be selected and analysis to be done for the task FRDPARRC format
Report and software analysis to be done, Report to be addressed in 3000 words and sample report attached Course material and lecture notes attached https://studentutsedu-my.sharepoint.com/:f:/g/personal/gopal-1_student_uts_edu_au/Ejnah7LDZkBDuFdy41PAfaEBb5RL1sRW5WM-xMQp9TViFQ?e=8DwhBu
Artefacts selected-
1)couplers Mechanical
2)locomotion part Mechanical
3)fasteners Mechanical
4)prototyping phase theoretical
Assignment Solution/Sample Answer
Note: For this assignment, All the Images will be provided along with the complete sample report once you will pay 6 USD charges.
2021 Warman Prototype Designs
Abstract
This paper offers a summary of the Warman Design and Build challenge project, as well as a look at and study the study and planning procedures that go into making a functional robot. For the purposes of this paper, the robot design process will be broken down into five artefacts: Base Assembly, Robot Motion Mechanisms, Track Width, and Wheels Motor. The reasoning, calculations, and investigation of the design will be studied throughout the artifacts to guarantee that the whole design process produces a product design that performs safely and reliably according the utilisation purpose as stated in its functionality. The investigation and brainstorming process will be used to back up the design judgments made on the basis of the functionality, providing additional clarity as to why each company intends and each alternative was chosen. The robot met the functional criteria relatively well, with possible hazards detected and remedies suggested as a consequence of the final results.
Artefact 1 – Couplers Mechanical 11
Artefact 2 – locomotion part Mechanical 13
Artefact 3 – Fasteners Mechanical 14
Artefact 4 – Prototyping phase theoretical 15
Economic Analysis and Feasibility: 16
Introduction
The sections listed below in this chapter of the article will outline the details of the competing and the report in order to provide context for what this proposal and, by extension, the report is about, as well as what data and/or guidance are used as the foundation for the project develop – construct. Competition for Warman Engineers Australia hosts the Warman Contest, a design and build competition in which universities from all across Australia compete. This contest was created to provide students more hands-on experience with innovative thinking, real engineering design, and building. The challenge of the competition has always been to build a vehicle or robot to convey products in some form or another, with varied conditions and particular aims and needs that vary from year to year. The following are the particular specifics and background of the hypothetical circumstance in which students must create for this year’s contest, which would be the 34th Warman Design & Construct contest. A self-contained mechanism for the deployment of active ingredients is required. The device will distribute 10 pallets of chemically neutralized substances to four refining plant silos. Due to the differing chemical depths in the four silos, different amounts of pallets are required. The pallets must be deployed quickly and must not come into touch with the hazardous surfaces inside the bunded region, and the device must also be returned quickly to avoid irreversible damage.
Objectives/Goals
In a laboratory setting, design, develop, and demonstrate a pallet deployment system proof-of-concept scaled prototype. • When the autonomous system starts totally within the Start/End zone and distributes pellets to each of the four tubes, points will be awarded. • As shown in Figure 1, the number of pellets to be placed at each silo is 3 for Silo A, 1 for Silo B, 4 for Silo C, and 2 for Silo D. • Additional points will be awarded if the entire system returns to the Start/End zone side of the bright black line in less than 120 seconds, with quicker systems being preferable.
Requirements
The exact needs for the competitive system are enormous, wide, and specific at the same time. The following requirements will outline the most important factors that will influence how the robot’s design is understood. • The system must not be dangerous. (i.e., the use of any type of combustion system is prohibited.) • Prior to commencing motion with no payloads, robots must not exceed the dimensions of 500x500x500 mm (w x d x h). • The system’s operation must come to a halt in 120 seconds. • To be judged successful, the system must be floor (i.e. no flying/must stay in contact with the competition track), and all 10 payloads must be dropped.
Materials: • MDF Sheet 300x300x12mm • Aluminium square tubing, length 125mm • Aluminium Bracket • Necessary Screws.
Materials: • Steel supports x2, largest size 25.4×25.4 • Motor with rack and gear • Aluminium spacers
Components: • Cardboard slide • Alloy Scissor-type extension • Bolt and slot drive • Stepper motor Dimensions: • Retracted: 450mmx200mm • Extended: 1900mm.
Materials: • Storage container – abs plastic • Fins for fan – Balsa Wood • 12mm steel rod • Servo motor • Coupler.
Wheels Click to add text Arduino Dc motor with wheels and rubber tires • It comes with a SG90 servo motor which power up to 4.8 Volts. • Easy to program in prototype. • Cost effective.
Electrical Hardware: Control Unit and Power • The Arduino Uno is chosen as the control unit (left). • This is powered by an external power source in autonomous functionality, in the case of this project there at 2 9-volt batteries connected to the circuit.
Electrical Hardware: Motors The motors in charge of the precise movement are: • Servo motors (left) • Stepper motors (right).
Acknowledgements:
Although every team member participated and is accountable for various components and systems/sub-systems of the robot, they all worked together to make it a reality. This project can only be completed with the will and collaborative work of my fellow group members, and it is by no means an isolated endeavour. The group had put in a lot of time and effort to make this happen and push through obstacles in the project, especially given the present scenario when some of us are physically unable to attend (myself including). My other group members deserve a great thank you for making all of this achievable.
Planning and research
The above part of the report will highlight the key details in areas that are the foundation of the design specifications and go in-depth on several of the preliminary choices taken and the intestinal fortitude of the project structure in terms of the design metrics, risk assessment, and entire project making plans for the automaton build project. This part will include both original and shared information that will be the same everywhere members of a group.
FRDPARRC is an important design tool that is used to validate design decisions and serve as the foundation for a design stage that can be linked back and linked to each design phase of the project. The FRDPARRC table presented below is a shared resource that was created as a collaborative effort.
Analysis and Design
The crew created a number of designs in the early phases of the project that would eventually lead to the ultimate concept of the robot they are building. In terms of the robot design stage, this conception stage is a collaborative group effort that pulls together ideas and serves as the foundation of our thinking process.
So instead traveling sideways to line with the silos, the platform will be stationary in the middle and travel at an angle from the centre of the base, before extending the belt to discharge the balls.
Analysis of Prototypes As an early design idea for the robot functions, three prototypes were created. One design will be picked from these three prototypes utilising multiple filtering processes to honestly choose the finest design for the project. A PUGH assessment and a Pros and Disadvantages table will be utilised in this scenario to find the best solution for the
project.
Gantt chart:
The Gantt Chart that was used to keep the project on track and as a guideline for what needed to be done at any given point throughout the project is discussed in the next section
Prototype Final
Following the completion of the project’s stages of development. It was decided to employ a final prototype. Although the final prototype differed from the prototype 1 described in the preceding section of the report. The core mechanism remains the same, with the pellets delivery game’s mechanism being changed from a chain-based system to a scissor lift mechanism owing to the process difficulties and low resource availability.
Overall System Design:
System Architecture Individual parts and components are required for the robot to function, and these parts and components are present to perform any combination of functions required by the system. This section should ideally be divided into two parts: mechanical and electrical components. However, the robot’s parts and components are generally employed in conjunction with other connected parts to build a sub-system. As a result, the primary pieces with mechanical and electrical components are given below.
NEMA 23 Motor – Wheel Shaft The driving engine for the wheel shaft is a NEMA 23 motor, which allows the robot to move in a transverse manner.
Scissor Lift – NEMA 17 Motor
The NEMA 17 motor is used in the scissor list mechanism, which raises the scissor lift to let it to move ahead and reach the intended objective.
Ball Dispenser
Dispenser of Balls To get the ball to the designated position, the ball dispenser releases it to the scissor lift.
Individual Electrical Components
Electrical Components on Their Own This system’s electrical components include motors and an Arduino board, which serves as the robot’s brain and controls all of the robot’s electrical activities.
Artefact 1 – Couplers Mechanical
introduction and SLOs That Matter The robot’s foundation is the foundation of the entire robot. This assembly will hold all other subassembly components and will allow the robot to move about so that the payload can be dispensed in the proper order. Sections 2 and 3 are the most important SLOs for this artefact because it will hold all of the robot’s other components and subassemblies. Design intent is necessary to guarantee that everything fits together correctly, and dimensioning is also important to fulfil the dimension restrictions.
The goal is to maximise dimension within the size constraints so that the base assembly can fit all components required for the robot’s proper operation. The same materials will be used for the base as for the SHS steel. Square tubes will be simple to construct and process, which will cut down on the time it takes to put the robot together. To boost stability, the first concept consisted of simply building a box with wheels mounted on the exterior of the chassis. However, after discussing how the payload dispensing mechanism will operate, it is altered to a three-level box that will house the electrical components as well as the payload dispensing mechanism.
Parameters of Design:
The following are the relevant quantitative and qualitative design parameters that will satisfy the assembly’s functional requirements: 1. The base assembly’s overall dimensions must not exceed 500 x 500 x 500. 2. The entire base assembly must fit inside the components. 3. The competition track must be completely covered by the base. 4. It must be able to travel in only one direction.
Analysis:
1.The following analysis will support the above-mentioned design parameters. The numbers in the analysis correspond to the design parameters that they correspond to. 1. The wheels will be positioned outside the base frame to enhance stability. The wheel shaft will be 500 mm long in order to maximise the dimensions. The frame is also 500mm long from end to end to guarantee that the maximum amount of space is available for the robot’s electrical components. With a wheel diameter of 100mm, the wheels do not surpass the length of the frame, thus they do not add to the frame length, which is already 500mm long. When it comes to the height, it’s reduced to 350mm, leaving 150mm for the payload dispenser mechanism.
2. The lower section of the base assembly is divided into two sections to ensure that the components fit inside. The scissor lift mechanism will be put in the centre, and the electrical components of the robot will be housed in the area left on both sides.
3. The design is based on a moving chassis that stays on the ground, ensuring that the base is fully in contact with the competition track. Four wheels are employed to maximise stability and room for the robot’s components.
4. With the decision to use a scissor lift mechanism to transport the payloads to their designated silos, the base is constructed with fixed wheels that allow it to only move in one axis. The design and construction of the base assembly will be simplified as a result. This will also make programming the robot’s movement easier.
Reference and Research:
A wind-powered vehicle that my team and I developed in Introduction to Mechanical and Mechatronics Engineering a few semesters ago served as inspiration for this concept. I’ve demonstrated that the design is solid and can withstand a lot of pressure.
Artefact 2 – locomotion part Mechanical
Introduction and Key Performance Indicators (KPIs) The robot’s wheels and other components will allow it to navigate around the competition track, allowing it to reach the desired silos and drop the pellets. Sections 3, 4, and 5 are the most important SLOs for this artefact since the wheels and related components in the robot’s movement mechanism require precise dimensioning to meet the size limits. Requirements for Function ‘The robot shall represent a ground-based solution’ and ‘the robot shall not exceed 500 x 500 x 500 mm in dimension’ will be the primary functional requirements for this artefact.
Selection and Ideation:
The limits of the project come first when it comes to ideation and wheel selection. To make the robot straightforward to construct, parts for the robot’s movement mechanism must be easily accessible and not over-spec’d to prevent exceeding the project’s budgetary constraints. With these considerations in mind, the robot’s wheels were chosen as ‘Ambassador 100mm White Plastic Centre Wheel and Rubber Tyre,’ with four wheels as mentioned in the previous artefact. These wheels will then be attached to the base assembly using a 10mm threaded rod and six 10mm bolts to connect the two wheels. After that, the wheel sets will be attached to the base assembly.
The choice of this robot movement system is one of the controlling factors of the robot design because the parts contained in this assembly are something we have few controls over because they are all ready-made parts and the only part that can be altered in this assembly is the 10mm threaded rod, which can be cut to any desired length. The wheel shaft will be reduced to 500mm in order to maximise the vehicle’s dimensions while still adhering to the competition’s dimensions. Parameters of Design The following are the relevant quantitative and qualitative design parameters that will satisfy the assembly’s functional requirements:
1. Accessible parts and components are required.
2. Dimensions must not exceed the authorised maximum.
3. The robot must be able to move thanks to the movement system.
Artefact 3 – Fasteners Mechanical
Track Width Introduction and Relevant SLOs (Artefact 3) As shown in the preceding artefacts, the robot’s track width was set to be as far away from the robot base as feasible in order to maximise the robot’s dimensions. This was done because it provides stability. This object will have a justification. Because the track width design is based on logical reasoning and will be justified using theories and calculations, the most relevant SLOs for this item are sections 3, 4, and 7. Requirements for Function ‘Comply with dimension constraints,’ ‘the system must fit with the overall design of the robot,’ and ‘the system must offer stability’ will be the fundamental functional criteria of the track width. These functional requirements are critical to the system’s design in order to ensure that the track width of the system provides stability to the robot and that it can work with the robot without interfering with other systems in the robot.
Selection and Ideation The system of this object was inspired by high-performance automobiles. A difference in track width can be noted when comparing normal passenger cars versus performance cars. Performance cars always have a wide track width, which helps them maintain stability and manoeuvre at high speeds. Although our robot will not be designed to perform extreme manoeuvres or travel at high speeds, the concept of a wider track width providing stability can still be applied to this system. Parameters of Design The following are the relevant quantitative and qualitative design parameters that will satisfy the assembly’s functional requirements:
1. Comply with the system’s dimensions limits.
2. Ensure that the system is as stable as feasible.
3. It must be small enough to take up the least amount of space in the overall system.
The following analysis will support the above-mentioned design parameters. The numbers in the analysis correspond to the design parameters that they correspond to. 1. The system’s design is 500 mm in length. This indicates that the system adheres to the dimensional restrictions. 2. Any given body’s centre of gravity is in its geometric centre. As a result, placing the wheel’s tracks at the robot’s farthest point will provide the most stability because it will decrease the total robot’s centre of gravity. 3. Because the wheel diameter is 100 mm and the wheel centre is 50 mm, the design of the system will be minimally impacted.
Artefact 4 – Prototyping phase theoretical
The wheel motor is responsible for rotating the wheel shaft and allowing the robot to navigate the competition course. The motor chosen is critical since it will affect the robot’s capacity to move. A motor with insufficient torque will prevent the robot from moving, while a motor with excessive torque will make the robot difficult to control and expensive. Sections 5 and 6 are relevant SLOs for this artefact since the motor selection process necessitates estimates on how much torque is required for the robot.
Requirements for Function The wheel motor’s primary functional needs will be “to deliver appropriate torque for the robot” and “to be able to be integrated into the system.” These functional requirements will indicate the motor’s ability to work with the robot while remaining economical, ensuring that the project does not exceed its budget.
Selection and Ideation:
Selection and Ideation The concept for selecting a motor is similar to what is stated in item 2. This technology will transmit power to the wheels via a mechanism similar to that used in front-wheel-drive automobiles. With that in mind, it’s simply a matter of choosing the correct robot motor. Parameters of Design The following are the relevant quantitative and qualitative design parameters that will satisfy the assembly’s functional requirements: 1. Provide sufficient torque to the robot. 2. It’s possible to incorporate it into the robot’s design. 3. Be cost-effective.
The following analysis will support the above-mentioned design parameters. The numbers in the analysis correspond to the design parameters that they correspond to. 1. The motor provides appropriate torque to the system, as computed in item 2, thanks to the torque multiplication effect given by the gears. 2. The NEMA 23 motor fits perfectly in our robot and can be mounted just above the wheel set, allowing for more direct power transmission. 3. The NEMA 23 motor fits neatly inside our budget at A$ 33.95.
Economic Analysis and Feasibility:
The cost analysis is critical to the project because it shows how costs are properly controlled throughout the project and how it avoids becoming a theoretical design.
References:
Baconnier, Y., Dupin, J., Guinand, R., Kissler, K. H., Middelkoop, W. C., Paillard, G., … & Zanasco, J. P. (1984). High-frequency magnet for separating beams in colliders. Le Journal de Physique Colloques, 45(C1), C1-297.
Bulatewicz, T., Cuny, J., & Warman, M. (2020, December). The potential coupling interface: Metadata for model coupling. In Proceedings of the 2004 Winter Simulation Conference, 2004. (Vol. 1). IEEE.
Harris, J., & Rimell, J. (2020). Can rapid prototyping ever become a routine feature in general dental practice?. Dental update, 29(10), 482-486.
Molloy, O., Warman, E. A., & Tilley, S. (2019). Design for Manufacturing and Assembly: Concepts, architectures and implementation. Springer Science & Business Media.
Smith, W. F. (2020, August). A Pillar of Mechanical Engineering Design Education in Australia: 25 Years of the Warman Design and Build Competition. In International Design Engineering Technical Conferences and Computers and Information in Engineering Conference (Vol. 55843, p. V001T04A003). American Society of Mechanical Engineers.
Warman, J. M., de Haas, M. P., Luthjens, L. H., Yao, T., Navarro-Campos, J., Yuksel, S., … & Houter, J. (2019). FluoroTome 1: An apparatus for tomographic imaging of radio-fluorogenic (RFG) gels. Polymers, 11(11), 1729.
Mechanical design 1 (48600) 2021 Warman Prototype Designs
Download the sample solution for the above-mentioned assignment or order a fresh assignment. We are ready to do it for you.
Click on the below button and mention assignment ID UA514 to download the task after paying 6 USD only and support us.
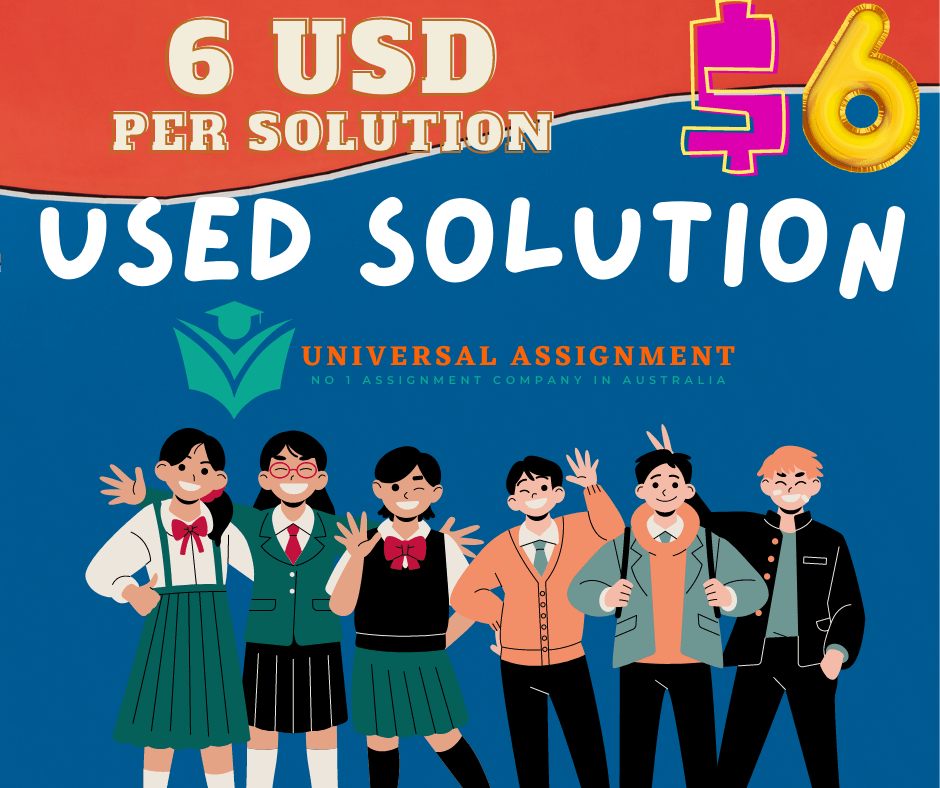